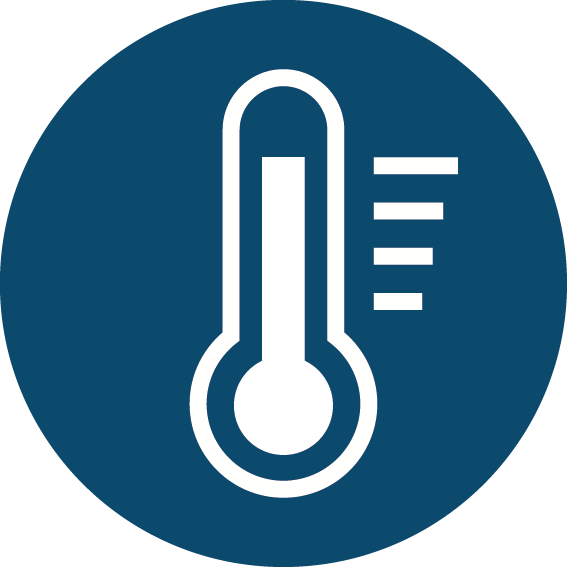
Stabilność cieplna
Stabilność cieplną materiałów można podzielić na strukturalną i chemiczną. W zależności od składu, powłoki PVD w obu trybach mogą wytrzymać temperatury od 300°C do ponad 1000°C.
Powłoki PVD: BIGAAN, LUBRIK G
Stabilność cieplna jest kluczowym parametrem opisującym zdolność materiału do zachowania swoich właściwości mechanicznych, fizycznych i chemicznych po wystawieniu na działanie podwyższonych temperatur przez określony czas. Jest to krytyczny parametr szczególnie w inżynierii materiałowej i zastosowaniach, w których materiał poddawany jest obciążeniom termicznym. Stabilność cieplną można podzielić na dwa podstawowe elementy: strukturalną stabilność cieplną i chemiczną stabilność cieplną.
- Strukturalna stabilność cieplna to zdolność materiału do zachowania mikrostruktury w podwyższonych temperaturach bez niepożądanych zmian, takich jak wzrost ziaren, zmiany składu fazowego lub procesy deformacji, które mogłyby wpłynąć na jego właściwości mechaniczne. Stabilność strukturalna jest więc ściśle związana z procesami dyfuzji i barierami energetycznymi dla zmian mikrostrukturalnych.
- Chemiczna stabilność cieplna dotyczy zdolności materiału do utrzymania swojego składu chemicznego i odporności na niepożądane reakcje chemiczne, takie jak utlenianie, azotowanie, nawęglanie lub inne formy degradacji, które mogą wystąpić w podwyższonych temperaturach. Stabilność ta jest ważna w przypadku materiałów narażonych na działanie agresywnego środowiska lub warunków korozyjnych.
W kontekście powłok PVD (Physical Vapor Deposition), które są stosowane w trudnych warunkach przemysłowych, stabilność cieplna jest kluczowym czynnikiem decydującym o ich trwałości i wydajności. W zależności od składu i rodzaju osadzania, powłoki PVD mogą wykazywać doskonałą stabilność cieplną, w zakresie od 300 °C do ponad 1000 °C. Stabilność taką uzyskuje się dzięki wysoce krystalicznym lub amorficznym strukturom, które ograniczają procesy dyfuzji i reakcje chemiczne.
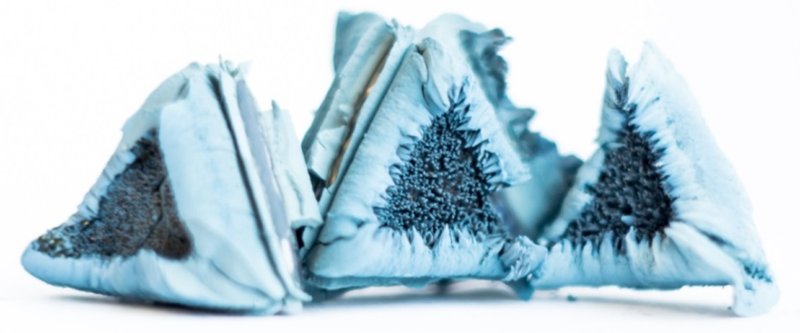
Pomiary
Najbardziej powszechnym sposobem oceny stabilności cieplnej jest pomiar twardości w różnych temperaturach wyżarzonych próbek. Jeśli wyżarzanie jest przeprowadzane w próżni lub w atmosferze ochronnej, jest to strukturalna stabilność „niechemiczna”. Większość powłok PVD bez problemu przetrwa temperaturę 400°C, a najlepsze z nich ponad 1100°C. Jeśli chodzi o rzeczywiste zastosowania, jest to trochę mylące, ponieważ musiałyby być stosowane w próżni lub atmosferze nieutleniającej. Znacznie bardziej realistyczne jest wyżarzanie w powietrzulub w powietrzu technologicznym. To znaczy z tlenem i parą wodną. Wartości te są często znacznie niższe, ale zoptymalizowane warstwy mogą również przetrwać temperatury powyżej 1000°C.Kompaktowe powłoki PVD są w stanie zapewnić skuteczną ochronę materiałów podłoża.
Rys.1 – temperaturowa zależność twardości i wielkości krystalitów warstwy nc-TiAlN/a-Si3N4 podczas wyżarzania w azocie (S.Veprek, Superhard and Functional Nanocomposites formed by Self-orginization in Comparison with Hardening of Coatings by Energetic Ion Bombardment during their DepositionRev.Adv.Mater.Sci 5 (2003), 6-16)
Bardzo interesującym przykładem kontrolowanej niestabilności cieplnej – oksydacyjnej jest powłoka CrVN. Zawartość wanadu kontroluje szybkość utleniania warstwy, która w wysokich temperaturach może tworzyć fazy Magnelliego. Fazy te znane są jako smary wysokotemperaturowe. Szczegóły opublikowano w artykule MM12/2015.