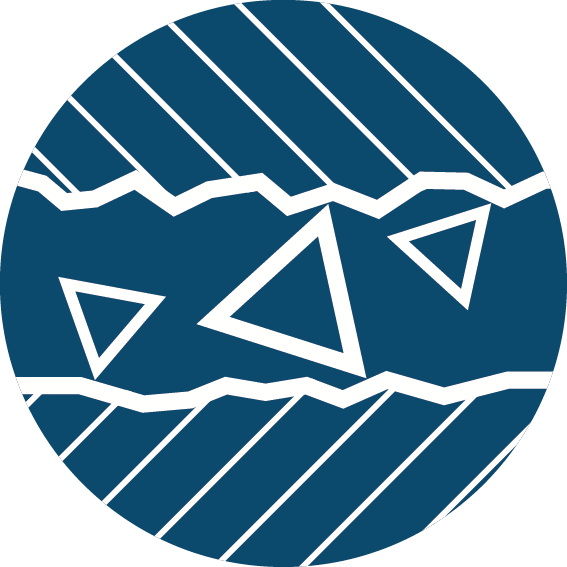
Odporność na ścieranie
Odporność materiału na niepożądane odkształcenia i ubytki powierzchni materiału w wyniku naprężeń mechanicznych, termicznych, chemicznych itp. Wraz z „powiązaną” z nią twardością jest to jedna z największych zalet powłok PVD.
Powłoki PVD: ALWIN XC
Odporność na ścieranie jest rozumiana jako odporność materiału na niepożądane odkształcenia i ubytki powierzchni z powodu połączonych naprężeń mechanicznych, termicznych itp. W rzeczywistości ten wszechstronny termin często odnosi się do odporności na szereg procesów degradacji, takich jak zużycie ścierne, adhezyjne, erozyjne, kawitacyjne, wibracyjne, zmęczeniowe i inne rodzaje zużycia eksploatacyjnego. W przypadku większości z tych rodzajów zużycia istotna jest jednak elastyczno-plastyczna reakcja materiału poddawanego naprężeniom, a także jego twardość. Odporność na ścieranie jest zatem bezpośrednio związanaz twardością. Przynajmniej w zastosowaniach o niskiej temperaturze kontaktu.
Większość naszych powłok została pierwotnie opracowana do obróbki skrawaniem i formowania, dlatego ich odporność na ścieranie jest wyjątkowa jak na ich grubość. Jeśli jednak z Twoich elementów znikają mikro- i milimetry, warstwa PVD ze względu na jej mikronową grubość nie będzie właściwym wyborem. Czasami pomóc może jeszcze połączenie z azotowaniem, lepsza obróbka cieplna lub materiał wyższej jakości.
Pomiary i wartości
Testy skrawania
Oznaczenie odporności na ścieranie lub ścieralności jest obok trwałości typowym parametrem w testach skrawania powlekanych narzędzi do obróbki. Rys. 1 przedstawia porównanie wielkości zużycia głównego ostrza płytki frezarskiej SPCN1204 podczas frezowania czołowego dla różnych wersji rozwojowych powłoki AlTiN. Na rys. 2 przedstawiono wspomniane starcie powierzchni.
Mikropiaskowanie
Kolejnym z wielu możliwych pomiarów odporności na ścieranie jest oznaczenie głębokości i objętości krateru powstałego w wyniku piaskowania. Do wytworzenia krateru użyto zaadaptowanej maszyny do mikropiaskowania, za materiał ścierny posłużyła siatka korundowa 500 a dawkowanie ścierniwa ustawione zostało na stałą objętość lub stały czas.
Rys. 3 przedstawia porównanie głębokości i objętości kraterów powstałych w wyniku mikropiaskowania różnych rodzajów stali i wersji powlekanych. Specjalistyczna warstwa na bazie węglika wolframu zapewnia bardzo skuteczną ochronę przed zużyciem ściernym.
Tribologia – zużycie
Inną dostępną metodą jest zastosowanie testów tarcia pin-on-disk w celu oceny stopnia zużycia kulki i toru.
Rys. 4 przedstawia porównanie zużycia/objętości toru tarcia dla różnych wersji powłok DLC. Metoda ta jest bardzo wrażliwa na poszczególne wersje powłok.
Aplikace
Nasze największe zastosowanie powłok PVD to 10 milionów powlekanych wymiennych płytek skrawających rocznie, głównie do frezowania. Od ponad 30 lat współpracujemy z firmą Dormer Pramet.