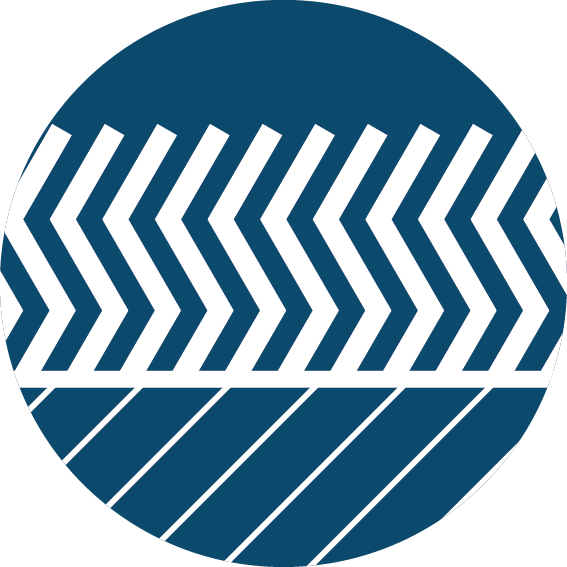
High specific surface area
This co-defines the efficiency of sorption processes, the chemical reactivity of solid substances and some catalytic processes. The PVD process allows the layers to be structured to provide a high specific surface area.
High specific surface area represents a key physico-chemical property of materials that indicates the total surface area of solids per unit mass or volume. This property is essential for a wide variety of physical, chemical and technological processes, including sorption (absorption, adsorption), catalytic and electrochemical reactions. The specific surface area affects the kinetics and thermodynamics of chemical reactions and thus directly co-determines the effectiveness of applications such as purification of gases, liquids, chemical synthesis, energy storage, or separation technology.
Materials with a high specific surface area generally have a better ability to interact with the surrounding environment because they offer a large active surface area for contacts with other molecules. In the context of sorption with processes such as absorption and adsorption, a high specific surface area allows for a greater number of active sites for the attachment of molecules from the surrounding medium. For example, with porous materials such as activated carbons, zeolites or mesoporous metal oxides, a high specific surface area is crucial for their use as adsorbents in processes for removing contaminants from water and air or in catalytic applications.
From the point of view of chemical reactivity, a high specific surface area is important for solids, as more exposed surface atoms or molecules means a higher number of active sites where chemical reactions can occur. This is particularly important in heterogeneous catalysis, where the catalytic reactions are confined to the surface layers of the catalyst. A high specific surface area enables a more intense interaction between the reactants and the catalyst, leading to higher catalytic activity and selectivity.
PVD technology represents a collection of methods that enable structural and morphological manipulation of materials at the atomic level, leading to the formation of layers with a very high specific surface area. PVD processes, such as evaporation, sputtering, and arc deposition, involve converting a material into a gas or plasma phase and then depositing atoms or molecules onto a substrate. This approach provides excellent control over layer thickness, composition, microstructure, and surface defect density, enabling targeted optimization of the materials’ physical and chemical properties.
Figure 1 shows the Thornton diagram modified by A. Anders showing the possibilities of structural modification of PVD coatings by changing process parameters.
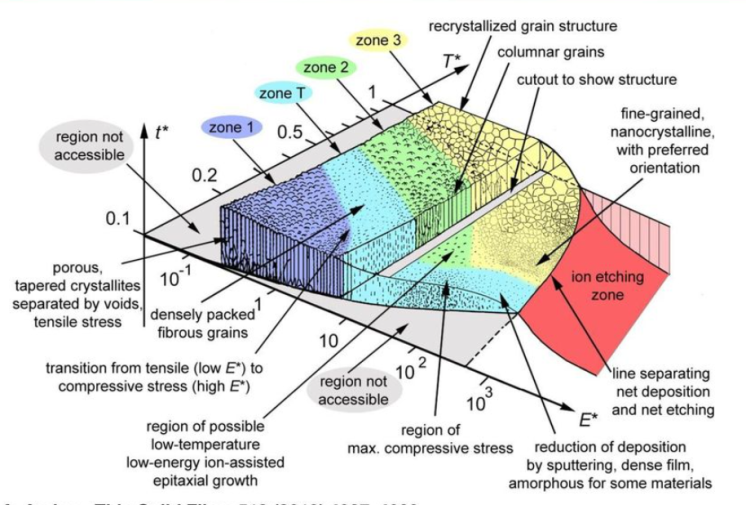
Fig.1 – Thornton’s modified diagram
(A.Anders, A structure zone Diagram including plasma-based deposition and ion etching, Thin Solid Films 518 (2010), 4087-4090)
Thanks to these capabilities, materials with unique properties such as nanostructured layers, thin films or multilayer structures with high specific surface area can be created through PVD. These layers can be optimised for various applications in areas such as electronics, optics, biomedicine or the development of new catalysts. For example, in the field of catalysis, layers with a high specific surface area can be used to increase the catalytic activity and stability of catalysts, while in sensor technology they enable higher sensitivity and selectivity of sensors for chemical and biological substances.