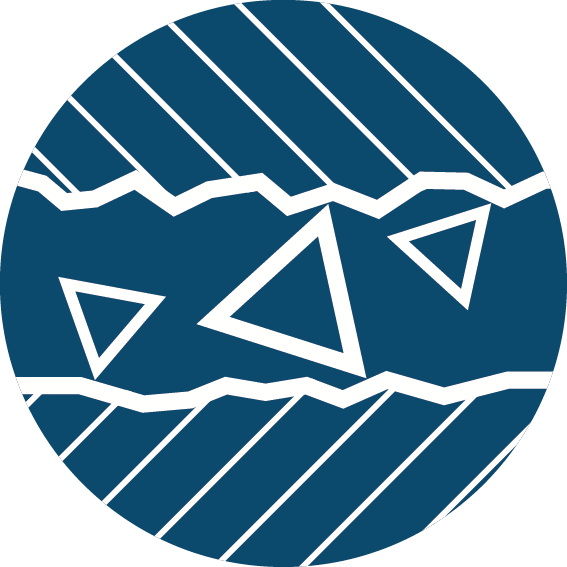
Abrasion resistance
The resistance of the material to unwanted deformation and losses to the material surface from mechanical, thermal, chemical, etc. stress. Along with the “relative” hardness, this is one of the greatest benefits of PVD coatings.
PVD coatings: ALWIN XC
Abrasion resistance is understood as the endurance of a material against undesirable deformation and surface loss due to combined mechanical, thermal, etc. stress. In fact, under this umbrella term we find the desired resistance to a number of degradation processes, such as abrasive, adhesive, erosive, cavitation, vibration, fatigue and other types of operational wear. However, for most of these types of wear, the elastic-plastic response of the stressed material and also its hardness are crucial. Abrasion resistance is therefore in direct relation to hardness. At least in low contact temperature applications.
The majority of our layers were originally created for machining and forming, therefore their abrasion resistance is extraordinary in relation to the thickness. However, if there are deviations of divisions of a millimeter in your parts, the PVD layer might not be an accurate fit due to its micron thickness. Sometimes a combination with nitriding, better heat treatment or better quality material can further help.
Measurements & Values
Cutting tests
The determination of abrasion resistance or abrasion is, in addition to durability, a typical parameter in cutting tests of coated machining tools. Fig. 1 is a comparison of the amount of abrasion of the main cutting edge of the SPCN1204 milling cutting insert during face milling for different development versions of the AlTiN coating. Fig.2 shows the aforementioned abrasion.
Micro sandblasting
Another of the many possible measurements of abrasion resistance is the determination of the depth and volume of the crater created by sandblasting. An extensively adapted micro-sandblaster was used to generate the crater, the abrasive was corundum mesh 500, and the dosage of the abrasive was constant volume or constant time.
Figure 3 shows a comparison of the depth and volume of the craters created by micro sandblasting of different steels and coated versions. A specialized layer based on tungsten carbide provides a very effective protection against abrasive wear.
Tribology – wear
Another possible way is to use pin-on-disk friction tests with an evaluation of the amount of ball and track wear.
Figure 4 shows a comparison of wear/friction path volume of different versions of DLC coatings. The method is very sensitive to individual versions of coatings.
Application
Our largest application of PVD coatings amounts to 10 million annually coated replaceable cutting inserts, mainly for milling. We have been working in cooperation with Dormer Pramet for over 30 years.