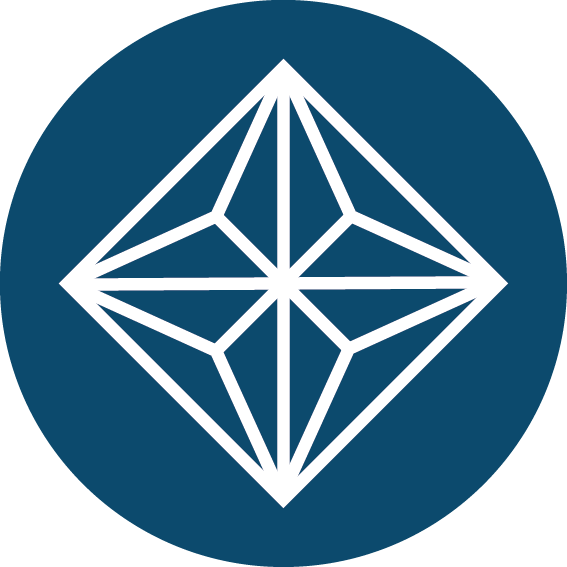
Twardość
Ogólnie rzecz biorąc, twardość można rozumieć jako odporność danego materiału na miejscowe odkształcenia plastyczne, czy też odporność na wnikanie ciała obcego w jego powierzchnię. Fizycznie zależy to od wielu właściwości charakterystycznych dla danego materiału, takich jak moduł Younga, odporność na pękanie, elastyczność itp. Z punktu widzenia zastosowania twardość jest zmienną determinującą odporność materiału na różnego rodzaju zużycie kontaktowe, takie jak zużycie ścierne, adhezyjne itp.
Powłoki PVD: TripleCoating SI, MARWIN SI
Twardość powłok PVD to prawdopodobnie ich najbardziej charakterystyczna cecha, która zależy przede wszystkim od ich składu. Niereaktywnie można przygotować bardzo miękkie, czysto metaliczne warstwy, a reaktywnie azotki, węgliki i tlenki o bardzo wysokiej twardości. Skład powłok można elegancko zmieszać lub stosować wymiennie, aby uzyskać pożądany efekt. Porównanie wartości warstw PVD z materiałami objętościowymi jest utrudnione ze względu na różne techniki pomiaru wynikające z ich mikronowych grubości. Powszechnie oznacza się je w odniesieniu do diamentu, który ma twardość około 100 GPa. Wersje metalowe około 4-8 GPa, zwykłe warstwy 15-40 GPa i najtwardsze 70-75 GPa. Z pewnym stopniem niedokładności, do ogólnego porównania można zastosować twardość Vickersa. 60 HRC stali hartowanych odpowiada w przybliżeniu 700 HV. Twardość diamentu wynosi około 10000 HV, a warstwy 1500 – 7500 HV. Powłoki PVD są nawet o rząd wielkości twardsze od stali hartowanej.
W przypadku niskich temperatur, bardzo odległych od temperatury topnienia obrabianych materiałów, jest to w bezpośredniej korelacji z odpornością na ścieranie. Z tego powodu twardość jest wykorzystywana jako podstawowa właściwość zamiast odporności na ścieranie podczas optymalizacji powłok PVD do obróbki skrawaniem i formowania.
Pomiary
Pomiar twardości cienkich warstw to świat sam w sobie. Metody te są instrumentalnie bardzo wymagające i wymagają dużej wiedzy. Stosuje się tu zmodyfikowane techniki wgłębiania podobne do pomiarów makrotwardości. Zamiast wielkości odcisku szczątkowego, mierzy się głębokość odcisku przy danym obciążeniu, a parametrymechaniczne są obliczane na podstawie krzywych obciążenia i odciążenia (rys. 1). Znanym ekspertem w dziedzinie pomiarów jest doc. Vilma Buršíková z Uniwersytetu Masaryka w Brnie.
Rysunek 1 przedstawia krzywe obciążenia materiału kalibracyjnego BK7 z urządzenia Fisherscope.
Rys. 2 przedstawia wgłębienie szczątkowe po mikrowgniataniu w hartowanej stali ČSN 19830.
Wartości
Do najtwardszych dostępnych na rynku powłok należą Ta-C przygotowywane metodą naparowywania łukowego i nanokompozyt nc-SiC/a-Cosadzany metodą napylania magnetronowego. Wartości twardości wynoszą około 75 GPa.
Warstwa | Mikrotwardość HV0.05 [GPa] | Moduł Younga [GPa] |
---|---|---|
Ti, Al, Cr, … | 3-6 | |
TiN | 26 | 530 |
TiCN | 47 | 490 |
TiSiN | 48 | 510 |
TiAIN | 45 | 360 |
nc-TiAlN/a-SiN | 48 | 400 |
TiC/C | 16 | 290 |
CrN | 24 | 380 |
CrNx | 20 | 350 |
CrVN | 30 | 440 |
AlCrSiN | 46 | 530 |
WC/C | 18 | 270 |
WCx | 34 | 415 |
SiBx | 35 | 380 |
nc-SiC/a-C | 70 | 480 |
A-C:H | 45-70 | 410-590 |
Typowe wartości niektórych warstw PVD do kalibracji wgłębnika na wzorzec BK7 przedstawiono w tabeli 1.
Referencje
- S. Veprek, Superhard and Functional Nanocomposites formed by Self-organization in comparison with Hardening of Coatings by Energetic Ion Bombardment during their Deposition, Rev.Ad.Mater.Sci. 5 (2003) 6-16,
- M. Jilek, O. Zindulka, Z. Studeny, Z. Pokorny, nc-SiC/a-C Coating for Industrial Applications, ICMCTF 2024.
Zastosowania
Wiercenie CFRP
Jednym z zastosowań bezpośrednio związanych z twardością/odpornością na ścieranie powłok PVD jest obróbka CFRP (Carbon Fibre Reinforced Plastic). Obróbka kompozytu wiąże się z intensywnym ścieraniem. Narzędzie zasadniczo nie tworzy wiórów, ale dochodzi do „wyszlifowania” kształtów. Do testu wybrano wiercenie, narzędziem było wiertło z węglika spiekanego o średnicy 8,5 mm, pokryte trzema rodzajami powłok – powłoką diamentową i powłoką nc-SiC/a-C o grubości 10 µm. Trzecią wersją była powłoka ta-C o typowej grubości ograniczonej naprężeniami wewnętrznymi wynoszącej 1 µm. Twardości wynosiły około 100 GPa dla diamentu, 68 GPa dla nanokompozytu i 55 GPa dla ta-C. Osiągnięta trwałość koreluje dość ściśle z twardością i grubością poszczególnych warstw.
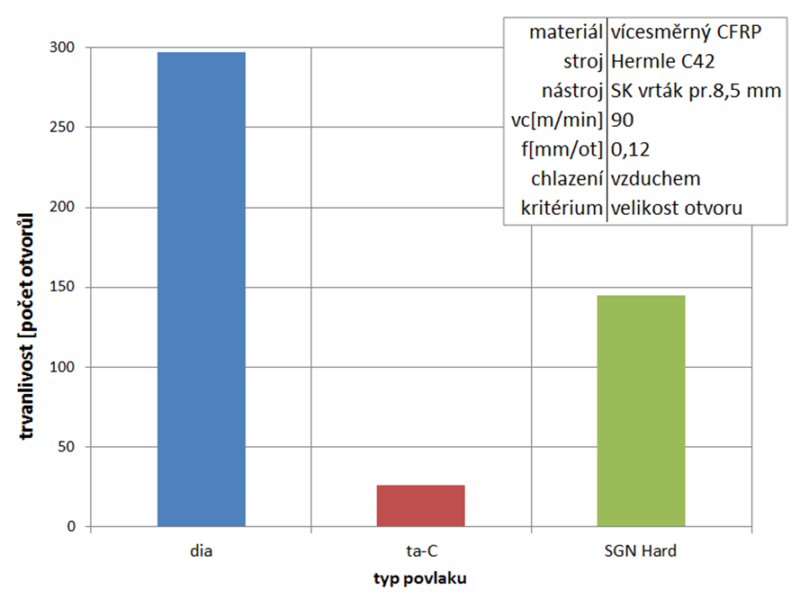
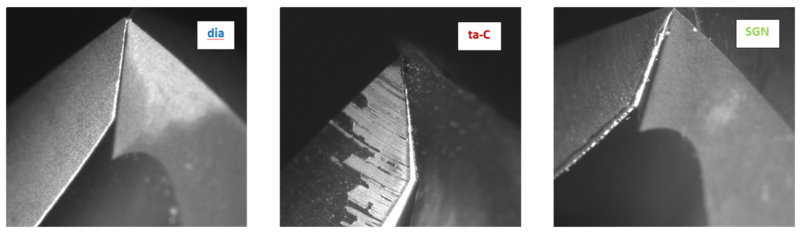